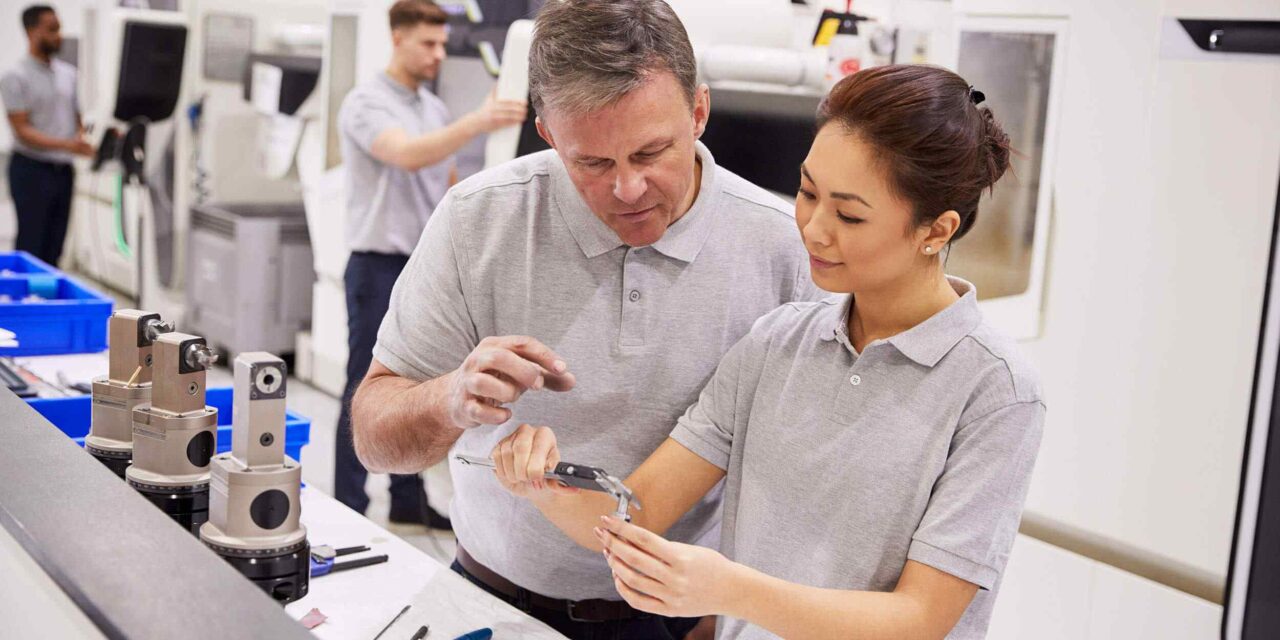
Problem:
In industries such as manufacturing, aerospace, and oil and gas, unplanned equipment failures can lead to significant downtime, costly repairs, and compromised safety. Traditional maintenance methods, which rely on fixed schedules or reactive approaches, often fail to detect early signs of equipment degradation, leading to unexpected breakdowns. This results in increased operational costs, reduced productivity, and potential safety hazards.

Our Solution:
Our AI-Powered Preventive Maintenance solution utilizes real-time monitoring and predictive analytics to detect early signs of equipment wear and prevent unexpected breakdowns. By optimizing maintenance schedules and extending equipment life, we ensure uninterrupted operations and enhanced safety.
Unlike standard solutions, this prototype is customized to each customer’s specific machinery, environment, and needs. If you’re interested, leave your details, and we’ll work together to develop a tailored solution for your factory.